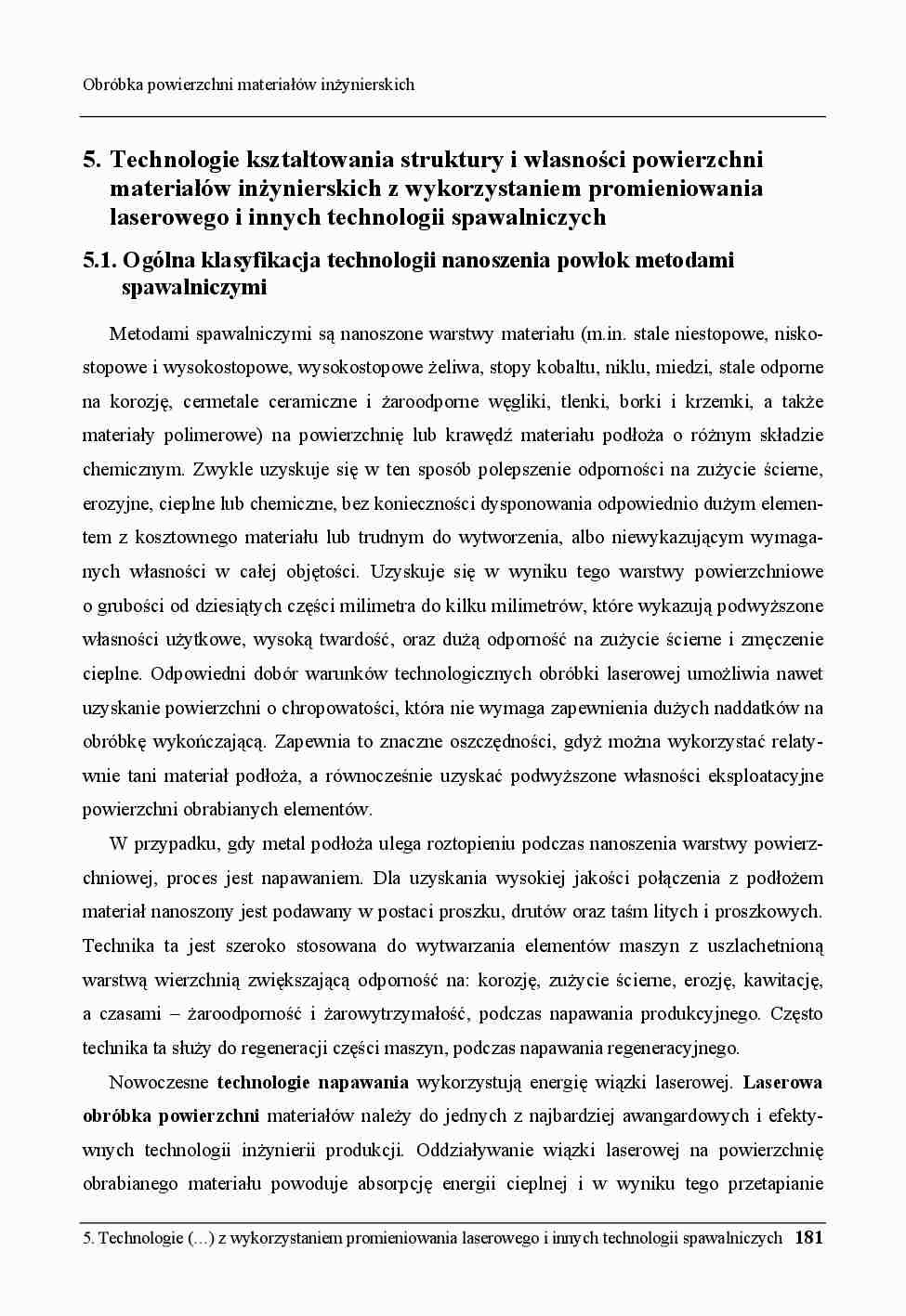
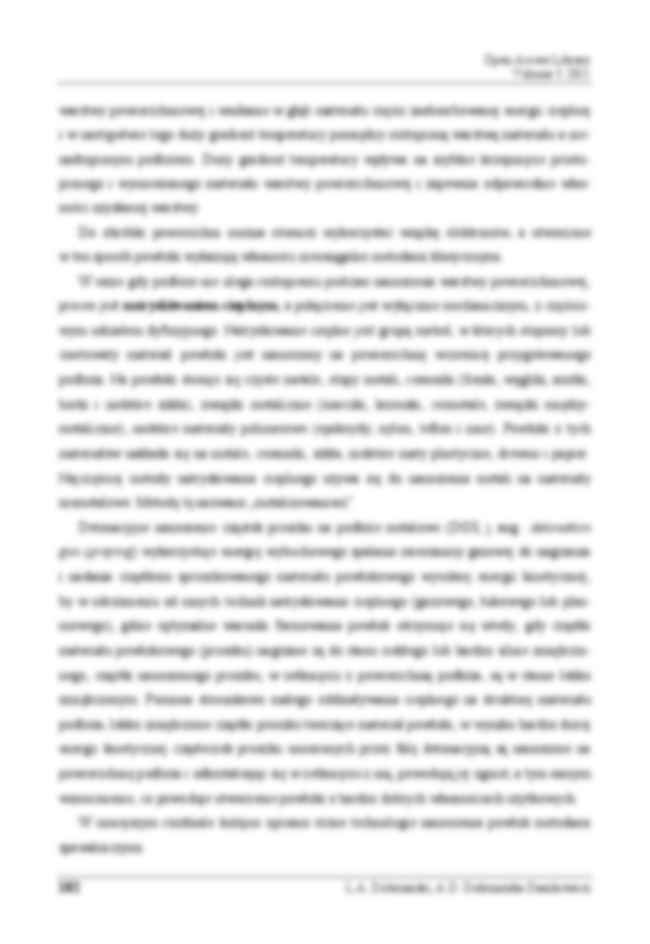
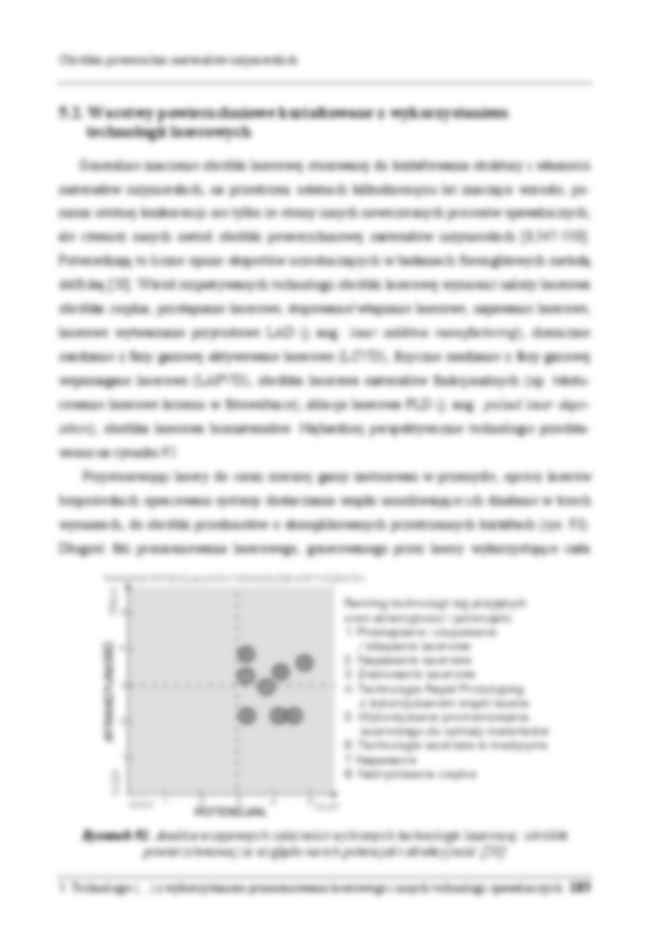
Fragment notatki:
Obróbka powierzchni materiałów inżynierskich
5. Technologie kształtowania struktury i własności powierzchni
materiałów inżynierskich z wykorzystaniem promieniowania
laserowego i innych technologii spawalniczych
5.1. Ogólna klasyfikacja technologii nanoszenia powłok metodami
spawalniczymi
Metodami spawalniczymi są nanoszone warstwy materiału (m.in. stale niestopowe, niskostopowe i wysokostopowe, wysokostopowe żeliwa, stopy kobaltu, niklu, miedzi, stale odporne
na korozję, cermetale ceramiczne i żaroodporne węgliki, tlenki, borki i krzemki, a także
materiały polimerowe) na powierzchnię lub krawędź materiału podłoża o różnym składzie
chemicznym. Zwykle uzyskuje się w ten sposób polepszenie odporności na zużycie ścierne,
erozyjne, cieplne lub chemiczne, bez konieczności dysponowania odpowiednio dużym elementem z kosztownego materiału lub trudnym do wytworzenia, albo niewykazującym wymaganych własności w całej objętości. Uzyskuje się w wyniku tego warstwy powierzchniowe
o grubości od dziesiątych części milimetra do kilku milimetrów, które wykazują podwyższone
własności użytkowe, wysoką twardość, oraz dużą odporność na zużycie ścierne i zmęczenie
cieplne. Odpowiedni dobór warunków technologicznych obróbki laserowej umożliwia nawet
uzyskanie powierzchni o chropowatości, która nie wymaga zapewnienia dużych naddatków na
obróbkę wykończającą. Zapewnia to znaczne oszczędności, gdyż można wykorzystać relatywnie tani materiał podłoża, a równocześnie uzyskać podwyższone własności eksploatacyjne
powierzchni obrabianych elementów.
W przypadku, gdy metal podłoża ulega roztopieniu podczas nanoszenia warstwy powierzchniowej, proces jest napawaniem. Dla uzyskania wysokiej jakości połączenia z podłożem
materiał nanoszony jest podawany w postaci proszku, drutów oraz taśm litych i proszkowych.
Technika ta jest szeroko stosowana do wytwarzania elementów maszyn z uszlachetnioną
warstwą wierzchnią zwiększającą odporność na: korozję, zużycie ścierne, erozję, kawitację,
a czasami – żaroodporność i żarowytrzymałość, podczas napawania produkcyjnego. Często
technika ta służy do regeneracji części maszyn, podczas napawania regeneracyjnego.
Nowoczesne technologie napawania wykorzystują energię wiązki laserowej. Laserowa
obróbka powierzchni materiałów należy do jednych z najbardziej awangardowych i efektywnych technologii inżynierii produkcji. Oddziaływanie wiązki laserowej na powierzchnię
obrabianego materiału powoduje absorpcję energii cieplnej i w wyniku tego przetapianie
5. Technologie (…) z wykorzystaniem promieniowania laserowego i innych technologii spawalniczych 181
Open Access Library
Volume 5 2011
warstwy powierzchniowej i wnikanie w głąb materiału części zaabsorbowanej energii cieplnej
i w następstwie tego duży gradient temperatury pomiędzy roztopioną warstwą materiału a nienadtopionym podłożem. Duży gradient temperatury wpływa na szybkie krzepnięcie przetopionego i wymieszanego materiału warstwy powierzchniowej i zapewnia odpowiednie własności uzyskanej warstwy.
BRAK FOTOWOLTAIKI i wielu innych SLA SLS. Co to jest laser, z czego jest zbudowany, na jakich zasadach działa. Fotony itd. dendryty
Nowoczesne technologie napawania wykorzystują energię wiązki laserowej. Laserowa
obróbka powierzchni materiałów należy do jednych z najbardziej awangardowych i efektywnych
technologii inżynierii produkcji. Oddziaływanie wiązki laserowej na powierzchnię
obrabianego materiału powoduje absorpcję energii cieplnej i w wyniku tego przetapianie
warstwy powierzchniowej i wnikanie w głąb materiału części zaabsorbowanej energii cieplnej
i w następstwie tego duży gradient temperatury pomiędzy roztopioną warstwą materiału a nienadtopionym
podłożem. Duży gradient temperatury wpływa na szybkie krzepnięcie przetopionego
i wymieszanego materiału warstwy powierzchniowej i zapewnia odpowiednie własności
uzyskanej warstwy.
Do obróbki powierzchni można również wykorzystać wiązkę elektronów, a utworzone
w ten sposób powłoki wykazują własności nieosiągalne metodami klasycznymi.
W razie gdy podłoże nie ulega roztopieniu podczas nanoszenia warstwy powierzchniowej
5.2. Warstwy powierzchniowe kształtowane z wykorzystaniem
Wśród rozpatrywanych technologii obróbki laserowej wymienić należy
Laserowa obróbka cieplna, przetapianie laserowe, Przetapianiu laserowemu warstwy powierzchniowej towarzyszy powstawanie plazmy
i parowanie materiału. Plazma ekranuje powierzchnię przed dalszym nagrzewaniem laserowym,
aktywnie oddziałując równocześnie na powierzchnię jeziorka ciekłego materiału przez
zwiększanie ciśnienia i mieszanie roztopionego materiału. W miejscu wnikania wiązki laserowej,
w jeziorku powstaje lejkowate zagłębienie, na którego powierzchnię działa ciśnienie
hydrostatyczne cieczy od strony roztopionego materiału oraz ciśnienie par od strony wiązki.
Chwiejna równowaga między tymi oddziaływaniami jest nieustannie zaburzana, między
innymi przez względny ruch obrabianego elementu i wiązki laserowej. W wyniku tego
następuje ruch względny zagłębienia w stronę nieroztopionego materiału, czyli przeciwnie do
ruchu elementu względem wiązki. Ciśnienie par powoduje wypełnienie zagłębienia po jego
przesunięciu się. Procesowi towarzyszy jednak powstanie charakterystycznej wypływki na
obrzeżu przetopienia Na powierzchni przetopionego materiału występuje więc pofałdowanie,
podobne do występujących na spoinach spawalniczych. Wymieniony efekt może być
osłabiony przez zdmuchiwanie plazmy przez gaz obojętny, korzystnie przy powtórnym
NAWĘGLANIE
Nawęglanie jest zabiegiem obróbki cieplno-chemicznej polegającym na wzbogaceniu w węgiel strefy powierzchniowej stali niskowęglowej. Proces prowadzi się w temperaturach 850—950°C w zakresie istnienia austenitu. Optymalna zawartość węgla w warstwie po nawęglaniu powinna wahać się w granicach 0,8 —1,0%. Grubość warstwy nawęglonej, zależnie od warunków pracy i wymiarów przedmiotu, przeważnie wynosi 0,5—1,5 mm, a w uzasadnionych przypadkach nawet do 2,5 mm.
Celem procesu nawęglania uzupełnionego późniejszą obróbką cieplną (hartowaniem i niskim odpuszczaniem) jest uzyskanie twardej i odpornej na ścieranie powierzchni (55 — 62 HRC) z zachowaniem ciągliwego, o dostatecznej wytrzymałości - rdzenia. Najczęściej nawęglanie przeprowadza się w ośrodku stałym i gazowym. Ośrodkiem bezpośrednio nawęglającym jest w obu wypadkach gaz, z tym, że w pierwszym wypadku powstaje on z proszku otaczającego obrabiane przedmioty, w drugim zaś gaz doprowadza się do pieca z zewnątrz lub wytwarza z wprowadzonych do pieca ciekłych węglowodorów.
Nawęglanie w ośrodku stałym (proszkach)
Podstawowym składnikiem proszków do nawęglania jest węgiel drzewny w ilości 85 — 95%, i węglany: BaCO3, Na2CO3 lub CaCO3 w ilościach 5 — 15%. Węglany mogą występować w proszku grupowo lub pojedynczo. Najbardziej uniwersalnym i prostym pod względem składu jest proszek
zawierający 95% węgla drzewnego i 5% BaCO3. Proszek ten ma tę zaletę, że nie powoduje nadmiernego stężenia węgla w warstwie nawęglonej. Przy jego użyciu uzyskuje się powierzchniowe około 1-procentowe stężenie węgla. Proces nawęglania w ośrodku stałym składa się z następujących czynności:
• ułożenie przedmiotów w skrzynkach z mieszaniną proszkową,
• zamknięcie skrzyni pokrywą, jej uszczelnienie najczęściej gliną i wysuszenie,
• włożenie do pieca,
• wygrzewanie w temperaturze nawęglania,
• chłodzenie skrzynek na powietrzu.
Podczas wygrzewania w temperaturze nawęglania tlen z zawartego w skrzynce powietrza reaguje z węglem drzewnym zgodnie z reakcją 2C+O2→2CO Wytwarzający się tlenek węgla przy zetknięciu z powierzchnią stali rozkłada się według reakcji 2CO Ca t+CO2 Powstały aktywny atomowo węgiel (Cat) zostaje następnie zaadsorbowany na powierzchni stali i dyfunduje w jej warstwy powierzchniowe. Tlenek węgla wytwarza się także z reakcji węglanu baru z węglem drzewnym BaCO3 + C → BaO + 2CO Wytworzony w tej reakcji tlenek baru reaguje z dwutlenkiem węgla powstałym przy rozkładzie tlenku węgla BaO + CO2 → BaCO3, co prowadzi do ponownego powstania węglanu baru. Wynika z tego, ilość BaCO3 nie ulega zmianie w trakcie nawęglania. Zmniejsza się natomiast zawartość węgla drzewnego w mieszaninie proszkowej. Powoduje to zmniejszenie wraz ze wzrostem czasu potencjału węglowego1) w trakcie nawęglania. Czas nawęglania zależny jest od rodzaju stali, użytego proszku, a przede wszystkim od wymaganej grubości warstwy nawęglonej. Nawęglanie w proszkach stosuje się w produkcji jednostkowej lub małoseryjnej wówczas, gdy elementom nawęglonym, później hartowanym i odpuszczonym, nie stawia się wysokich wymagań. Bardziej nowoczesnym procesem
SPAWALNICTWO
Laserowa obróbka cieplna
części maszyn i urządzeń
PROF. ANDRZEJ KLIMPEL*, MGR INŻ. ALEKSANDER BOREK**
Technologia laserowej obróbki cieplnej daje możliwość dokładnej regulacji przemian strukturalnych, prowadząc do wyraźnego wzrostu własności trybologicznych materiałów. Technologia ta pozwala na obróbkę
trudno dostępnych i dowolnie dużych obszarów roboczych, będąc zarazem techniką efektywną ekonomicznie i przyjazną dla środowiska.
Szczególnym procesem obróbki warstw
wierzchnich części maszyn i urządzeń
za pomocą energii wiązki laserowej,
do których zalicza się również napawanie, stopowanie, przetapianie, jest
technologia laserowej obróbki cieplnej
[1-18] – rys. 1 do 10. Z uwagi na bardzo
złożoną problematykę badawczą, na pograniczu subtelnych badań strukturalnych inżynierii materiałowej i spawalniczych technologii laserowych, wymaga
ona dużej wiedzy w obszarze metaloznawstwa, metalurgii materiałów metalowych i ceramicznych oraz technologii
laserowych [1-3]. W procesie tym energia wiązki laserowej, o wysokiej gęstości mocy od ok. 10² [W/mm²] do nawet
105-106 [W/mm²], nagrzewa warstwę
wierzchnią obrabianego przedmiotu
o ściśle określonej grubości do wymaganej temperatury obróbki cieplnej, zwykle tuż poniżej solidus, w odpowiedniej osłonie gazowej, z prędkościami
nawet do 106-1011 [°C/s], po czym następuje samoczynne schładzanie warstwy z prędkościami dochodzącymi
do 105-106 [°C/s] [1, 2]. W ten sposób pod warstwami wierzchnimi powstaje strefa wpływu ciepła (SWC),
podobnie jak w procesach napawania,
stopowania czy przetapiania laserowego. Warstwy wierzchnie części maszyn i urządzeń wykonanych z metali
i stopów, których własności użytkowe
zależne są od stanu obróbki cieplnej,
można obrabiać cieplnie z wykorzystaniem energii promieniowania laserowego, uzyskując znacznie wyższe
własności użytkowe i efekty ekonomiczne niż w przypadku klasycznych
metod obróbki cieplnej [1-18].
Przemysł światowy coraz częściej stosuje w produkcji nowoczesnych części
maszyn i urządzeń technologię laserowej obróbki cieplnej, uznając wysokie
własności użytkowe warstw wierzchnich przedmiotów stalowych i żeliwnych wykonanych ze stopów niklu,
tytanu, kobaltu, a nawet miedzi i aluminium, obrobionych cieplnie energią
wiązki laserowej ciągłej lub impulsowej.
Istotna jest także ekonomiczność tego
procesu w stosunku do konwencjonalnych metod obróbki cieplnej. Laserowa obróbka cieplna umożliwia wykonanie warstw wierzchnich o dowolnym
kształcie i wielkości powierzchni na roboczych powierzchniach przedmiotów
o dowolnym kształcie i masie, podobnie
jak ma to miejsce w procesach napawania, przetapiania i stopowania laserowego warstw wierzchnich [1]. Nowoczesne urządzenia laserowe, a zwłaszcza
lasery na ciele stałym: Nd:YAG, diodowe, włóknowe i tarczowe, umożli-
0,2 m/min
AZOT
0,4 kW 0,6 kW 0,8 kW 1,0 kW 1,2 kW 1,4 kW
0,15 m/min
1,6 kW 1,8 kW 2,0 kW 2,0 kW
ARGON
0,15 m/min
0,1 m/min 0,2 m/min
2,0 kW 0,4 kW 0,6 kW 0,8 kW 1,0 kW 1,2 kW 1,4 kW 1,6 kW 1,8 kW 2,0 kW 2,0 kW
... zobacz całą notatkę
Komentarze użytkowników (0)